Plastic extrusion is a widely used manufacturing process for shaping plastics, particularly thermoplastics. It involves creating objects with continuous profiles, such as pipes, tubing, and door profiles. This article delves into the basics of plastic extrusion, including the process, materials used, products created, and a comparison with aluminum extrusion.
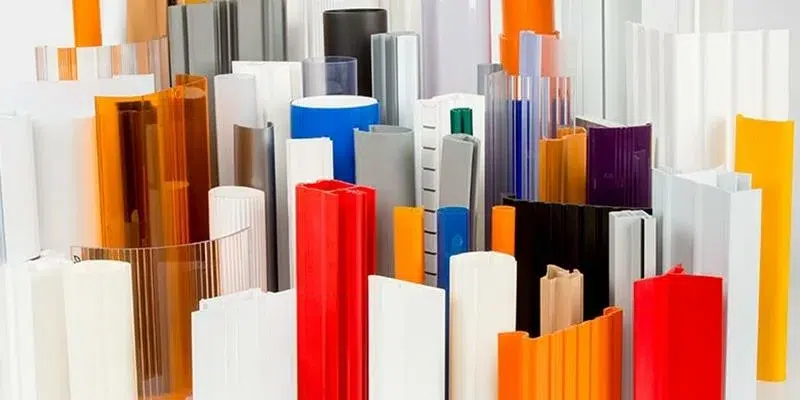
The Plastic Extrusion Process
To understand plastic extrusion, it’s essential to grasp the components and functioning of an extruder. Typically, an extruder consists of:
- Hopper: Holds the raw plastic material.
- Feedthroat: Allows the plastic to enter the barrel from the hopper.
- Heated Barrel: Contains a screw driven by a motor to force the material towards the die.
- Breaker Plate: Equipped with screens to filter the material and maintain pressure.
- Feedpipe: Delivers the molten material from the barrel to the die.
- Die: Shapes the material into the desired extrusion profile.
- Cooling System: Solidifies the extrusion evenly.
The process begins by filling the hopper with solid plastic pellets or flakes. Gravity feeds the material into the extruder barrel. Inside the barrel, the material is heated via multiple heat zones and simultaneously pushed towards the die by a reciprocating screw. The screw and pressure generate additional heat, reducing the reliance on the heat zones.
The molten plastic exits the barrel through a screen reinforced by the breaker plate. This screen removes contaminants and maintains pressure. The material then passes through a feedpipe into a custom-built die, which shapes it into the desired extrusion profile.
Once through the die, the extrusion profile is cooled in a water bath or via cooling rolls, causing it to solidify.
Extrusion Plastics
Plastic extrusion is compatible with various thermoplastics, which are heated to a temperature sufficient to melt the material without causing thermal decomposition. These materials are typically fed into the extruder as pellets, powders, flakes, or granules.
Common extrusion plastics include:
- Polyethylene (PE): Extruded between 400°C (low density) and 600°C (high density).
- Polystyrene (PS): ~450°C.
- Nylon: Between 450°C and 520°C.
- Polypropylene (PP): ~450°C.
- PVC: Between 350°C and 380°C.
In certain cases, elastomers or thermosets may be used instead of thermoplastics.
Plastic Extrusion Applications
Plastic extrusion companies produce various parts with consistent profiles. Some common applications include:
- Pipes and Tubing: Plastic piping and tubing, often made from PVC or other thermoplastics, are ideal for simple cylindrical profiles.
- Wire Insulation: Many thermoplastics offer excellent electrical insulation and thermal stability, making them suitable for wire and cable insulation and jacketing.
- Window and Door Profiles: Plastic door and window frames are well-suited to extrusion due to their continuous profile and length. PVC is a popular material for this application.
- Blinds: Window blinds consisting of identical slats can be extruded using thermoplastics. Polystyrene is commonly used for faux wooden venetian blinds.
- Weatherstripping: Plastic extrusion companies often make weatherstripping products, such as draft excluders, with profiles designed to fit closely to door and window frames. Rubbers are common weatherstripping materials.
- Windshield Wipers and Squeegees: Automobile windshield wipers and manual squeegee blades are often extruded using synthetic rubber materials like ethylene propylene diene methylene.
Plastic Extrusion vs. Aluminum Extrusion
In addition to thermoplastics, aluminum can also be extruded to create parts with continuous profiles. Aluminum extrusion offers advantages such as lightness, conductivity, and recyclability. Common aluminum extrusion applications include bars, tubes, wire, piping, fencing, tracks, frames, and heat sinks.
Unlike plastic extrusion, aluminum extrusion can be either hot or cold. Hot extrusion occurs at temperatures between 350°C and 500°C, while cold extrusion takes place at room temperature.